Condition-based maintenance of equipment
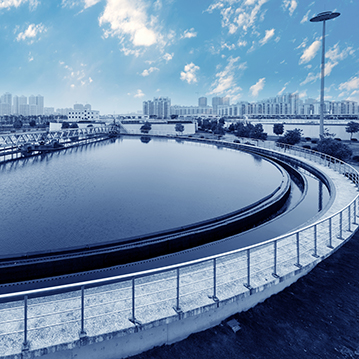
Multi-technical monitoring of equipment (vibration analysis, infrared thermography, electrical analysis, oil analysis, ultrasound) is offered to provide an overview of equipment health, for an effective maintenance policy.
Dynae provides consulting and training services upstream geared towards optimising condition-based maintenance.
Vibration and electrical diagnoses
Diagnoses should be considered on taking delivery of new facilities in order to check compliance and then be used as a benchmark.
This involves carrying out the electromechanical status check including the shaft lines and the motor, by means of a vibratory and electrical signature.
Then, vibration and electrical measurement campaigns will be considered periodically on critical equipment, in order to anticipate and organise maintenance work as well as possible.
In the event of a malfunction or anomaly, an S.O.S. diagnosis is carried out to find the cause of the fault.
Online vibration monitoring systems
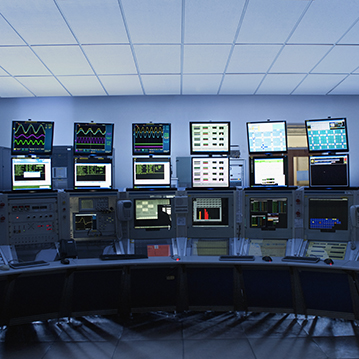
There are many solutions on the market; Dynae will study for you the one which will be best suited to the challenges and the budget involved.
After being configured and providing training, you will have a turnkey solution; it is an opening towards remote diagnoses and data aggregation for the factory of the future.
Support for new projects
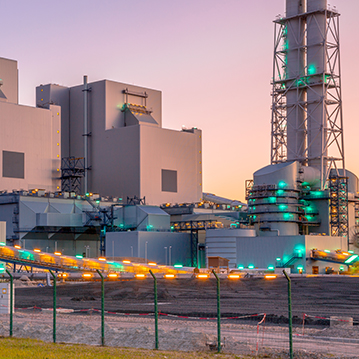
New units, new machines: We support you when it comes to anticipating the dynamic behaviour of equipment and avoiding resonance problems during commissioning.
Piping analysis is particularly important as soon as you have machines generating strong excitations (compressors, rotating machines).
The initial and electrical vibration signature of the machines in the start-up phase (acceptance test) will allow everything to be validated and a zero point to be established, which will serve as a benchmark.
Infrared thermography
Infrared thermography analysis is very widely used in this sector of activity. Indeed, energy saving challenges are at the heart of current process optimisation approaches.
In addition, types of production involving high temperatures at the heart of the process make the use of infrared thermography even more important.
It is particularly used to carry out the auditing of urban heating networks by airborne means (plane, helicopter, drone) in order to carry out leak tests, monitor the aging of networks, control heat losses and therefore improve the thermal efficiency of the network.
The handing over and then the thermographic monitoring of furnace, boiler and heat insulator walls also makes it possible to check for leaks and heat losses, refractory and thermal insulation issues and thus greatly improve the performance of the facilities, while helping to prioritize work.