Dynae generally relies on vibration measurement campaigns, supplemented if necessary by analyses of the motors’ feed currents, as well as infrared thermography. Oil analyses are carried out by our partner IESPM.
The aggregation of this data with a set of process data can be done to establish correlations and behaviour models useful for anticipation and decision making purposes.
Towards the factory of the future
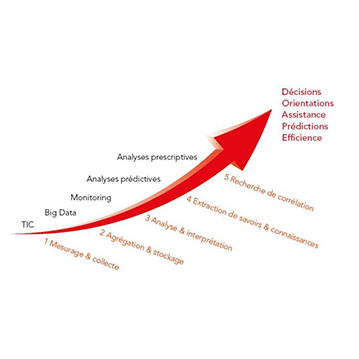
Dynae supports you as you head towards the factory of the future, with studies and demonstrators to incorporate dynamic analyses into prescriptive analysis processes.
Our advantages: cooperation with data scientists from the group's KM0 unit.
Vibration monitoring of rotating machines
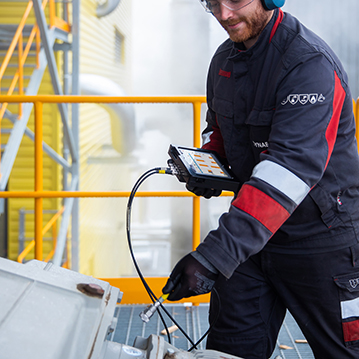
It is based on periodic or continuous measurements to fit into the forward-looking maintenance policy to optimise machine availability and reduce costs.
The vibration measurement is carried out using the CTMO®, which records the raw time signals on 4 channels. The DynamX Suivi® software processes these signals to extract the evolution curves of the monitoring indicators. In the event of an alarm, the signal will be reprocessed to carry out a diagnosis: cause of the fault, seriousness, recommended maintenance action.
It is also possible to remotely monitor a fleet of machines, by accessing the vibratory database via the Internet. Dynae then performs the analyses remotely.
Our advantages: Vibration analysis and current analysis
Current analysis
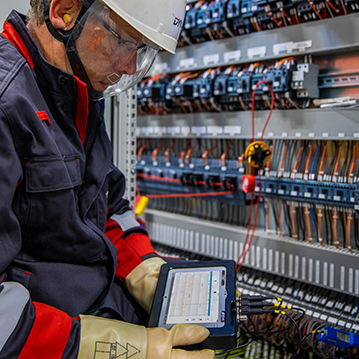
The purpose of measuring electrical signals is to detect the emergence of various faults, for the purpose of predictive maintenance:
- network-related faults: imbalances, cos Ø, harmonic distortion
- faults related to regulation or control: electrical disturbances, pumping, thyristors
- stator or rotor electromagnetic faults: short circuit, cracked bar
- certain mechanical faults in the shaft line: coupling play, keyway play, cardan joint fault, offsets, etc.
- some process-related faults
The measurement is carried out using current clamps connected to the CTMO® and the signals are then processed with DynAlim® to extract the indicators.
Our advantage: our dedicated tools
Multi-technical monitoring
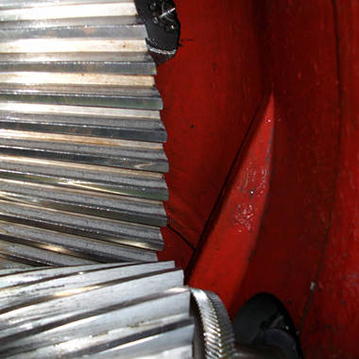
It makes it possible to optimise the maintenance policy by combining the use of complementary techniques: vibration analysis, electrical analysis, thermography, lubricant analysis (carried out in conjunction with our partner IESPM)
Grouping these inspections together into a comprehensive service has many advantages:
- It gives a snapshot at a particular time for the various techniques, which makes it possible to cross-reference the analyses to refine the diagnosis.
- It brings together the mechanical and electrical recommendations for each piece of equipment.
- It optimises the time and resources for the collection of the various measurements
Our advantage: the association of specialists